Love them or hate them, there is no getting away from the pipe detail!
It’s not often a roof doesn’t contain one, especially on refurbishment projects. They come in all shapes and sizes from small handrail posts, all the way through to large duct type pipes.
When installed well, they can finish the roof off perfectly.
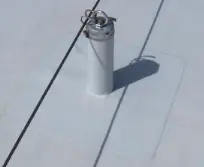
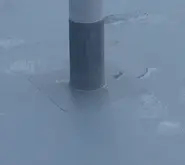
When installed badly, however, they can ruin the overall finish!
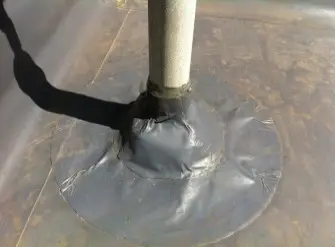
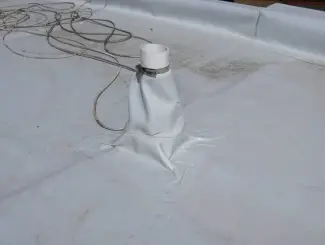
If you get a combination of bad workmanship and poor positioning, it can be a disaster!
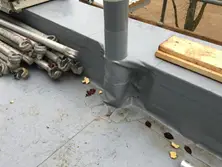
Ducting pipes can also be tricky to seal if they have a spiralling crimped joint. The joint will allow water to track down its seam and bypass any seal at the top of the pipe collar. The only effective way of sealing the pipe is to completely encapsulate the whole length of the pipe.
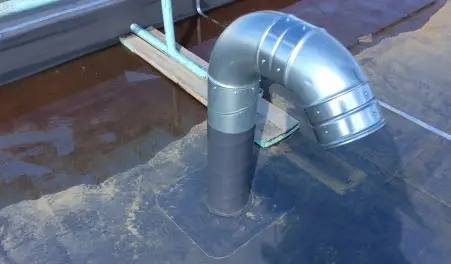
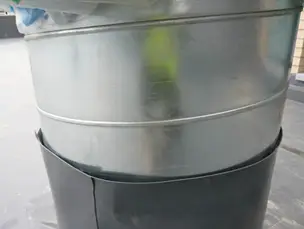
If it is a hot pipe over 80°C, then this would need to be isolated with some form of insulant and a secondary sheath as detailed below.
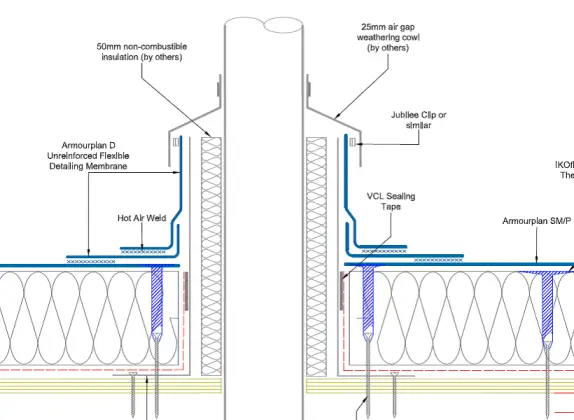
Regardless of their size or shape, they are nearly all detailed and weathered in the same way: apron, collar, clip & mastic seal.
A common error on site is the use of incorrect membrane to form the pipe details.
Both the apron and collar need to be heated and formed; you cannot do this with a polyester re-enforced membrane as the re-enforcement is designed to stop the membrane from stretching.
It is essential that the membrane needs to be either homogenous or have a glass tissue carrier.
Aprons
The apron is sometimes missed out but has two important roles to play. Firstly, when the field membrane is cut around, a pipe it is rarely trimmed close to the pipe leaving a gap between the cut edge and the pipe.
This creates a problem when installing the collar as the collar will typically only cover 20mm on to the field area resulting in insufficient overlap. The base plate central hole is cut 30% of the pipe diameter and stretched over the pipe ensuring that there is membrane around the base of the pipe. The upturn of the base plate will also act as a temporary seal.
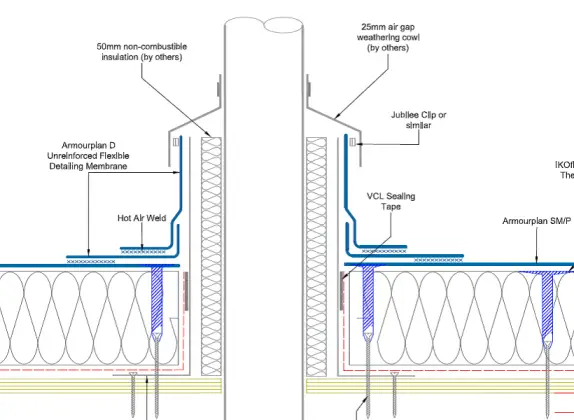
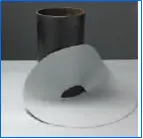
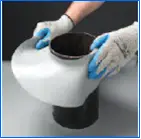
The second use for the base apron is to conceal any required additional fixings to isolate the pipe detail from membrane movement on mechanically fastened projects. The apron can be any size as you may not be able to install fixings close to the pipe. It is a good idea to keep the apron sizes consistent across the roof for the best aesthetical results.
If it is not possible to conceal the fixings within the apron, then it is recommended to weather the additional fixings with a cover strip. Again, it is best to try the fixing distance from the pipes uniform to aide aesthetics.
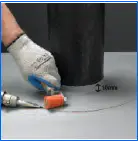
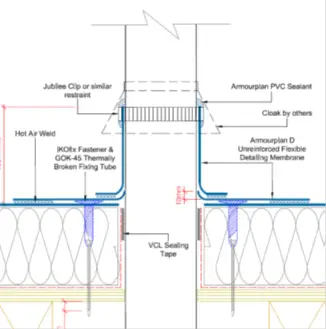
If a pipe is close to a row of membrane fasteners, then the pipe only needs to be isolated on the three-outward facing sides. If the pipe is more than 250mm from the membrane fasteners, then it is advisable to isolate the pipe on all sides.
Failure to isolate the pipe will result in the pipe collar being displaced from the pipe resulting in a failure.
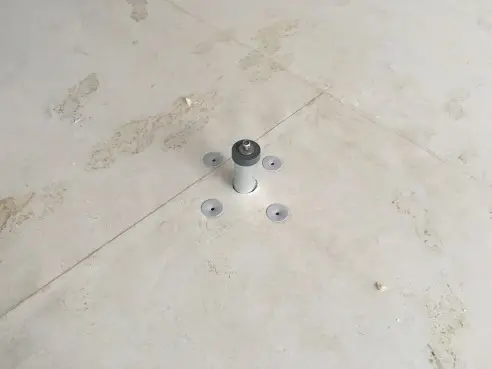
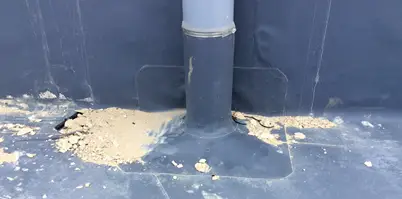
Collars
The size of the collar should allow for a 20mm vertical overlap, a 20mm overlap on to the field sheet and the length of the collars need to be 150mm above the height of the finished roof which includes decking and slabs etc.
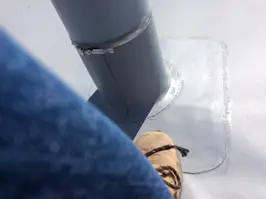
Once you have the correct sized collar, the next stage is very important. The bottom of the collar needs to be heated up and stretched so that it will splay out easily onto the apron. For best results, the stretched section should site easily onto the apron and not try to peel back upon itself. If it peels back on itself whilst you are trying to weld it down, it could result in a poor and untidy weld and worse still the membrane splitting.
The membrane can still split even when the collar has been prepared adequately. This can be very frustrating and is caused by the membrane becoming very hot and vulnerable during the welding process. The overlap weld is formed in the same way as a normal seam as in a pre-weld and a final weld.
I always advise that once the pre-weld has been completed the membrane is allowed time to cool and return to its normal temperature which takes a couple of minutes. Once cooled the final weld can be completed and this generally results in a split free weld.
Clip & mastic seal
Once the pipe has been weathered by membrane, the final job is to seal the top of the membrane to the pipe. If this is not executed correctly, all the hard work on the detail can be wasted.
There are several ways to seal the top of the pipe:
- Clip & mastic seal
This is the most common method especially on new build projects. The clips can be either a heavy-duty cable tie or the preferred method of a stainless-steel clip especially on extended warranty projects.
It is important that the mastic is either approved or supplied by the membrane manufacturer. This will ensure that there are no issues with compatibility, and it will not compromise the membrane manufacturer’s warranty.It is worth noting that generally the mastic element is considered a maintenance item and not guaranteed past 10 years.
- Clip & cowling
A cowling is a neat way of finishing of a pipe but not normally part of the roofing package if on a new build project. The pipe detail wouldn’t normally require a mastic seal at the point of the clip as the cowling would normally have a mastic seal.
However, if the cowling is being installed by a different supplier, it is advisable to apply your own mastic in case the cowling is not fitted soon after the pipe has been completed or if the mastic isn’t applied very well by the other trade.
Hot pipes are normally having this type of finish due to the nature of the collar not being tight to the pipe detail.

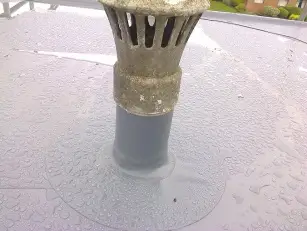
3. Clip & membrane sleeve
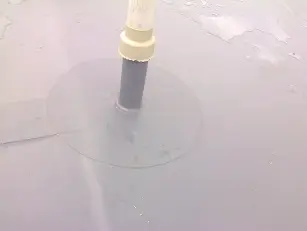
Shorter pipes can be terminated with the clip and a membrane sleeve. The membrane is taken to the top of the pipe and terminated with a clip.
A secondary sleeve is inserted tightly into the pipe by a minimum of 100mm and the membrane above the pipe needs to be about 50mm. This is then heated up and when pliable pulled back over the pipe clip and collar. The finished result is a neat and tidy pipe which does not require a mastic seal.
It is often the case that you will get multiple pipes in proximity which can be difficult to weather correctly. A useful tip is to create the pipes on a rig and then transfer them onto the actual pipes, leaving only the welding of the base plate.
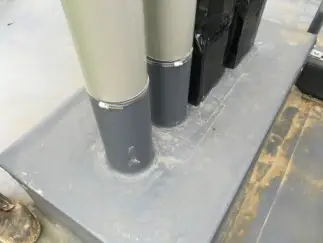
At IKO Polymeric we offer a unique service in producing pre-made pipes. The contractor sends in the dimensions of the pipes required and our Prefabrication Department will manufacture the pipe details for the contractor.
We can manufacture closed or open pipes for when the pipe cannot be slipped over the pipe, the open pipes can also come with a preinstalled overlap.
The details are high frequency welded on specialist equipment and all the welds are tested before being sent out to site.
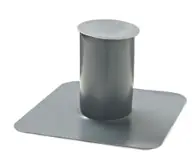
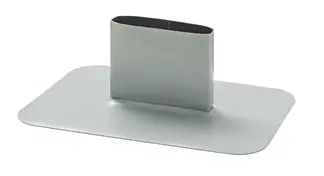
And finally, for that impossible pipe detail, we have our in-house liquid Polimar detailing solution.
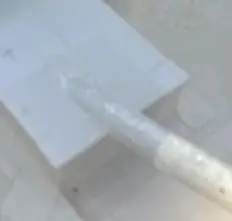
For more information, please contact IKO Polymeric’s Technical Team.
Phone: 01257 488 012