Exchange Square, Birmingham – IKO Permatec Anti-Root
Project description
Phase One of Exchange Square in Birmingham city centre is a stunning development of three tall buildings, offering over 60 luxury apartments, plus a 5,000 sq ft residents’ hub and prime retail and leisure space.
The development is by Nikal for La Salle Investment Management, located between the city’s traditional business and retail districts and the progressive Eastside, Exchange Square epitomises the area’s dramatic renaissance and has been dubbed a new urban village.
Robust and long-lasting systems were required for flat roofs, balconies and podiums. All roofs needed to meet stringent thermal performance standards – in this case a U-value of 0.2W/m2K – ideally without the use of insulation within the interior ceiling void.
Green roofs and ceramic paving were part of the specification while direct access from balconies into the apartments needed to be level.
With three buildings in close proximity and the tallest of the three being 27 storey the roof needed careful planning to take into account wind uplift, while the contractors also needed to contend with a tight build programme and limited access.
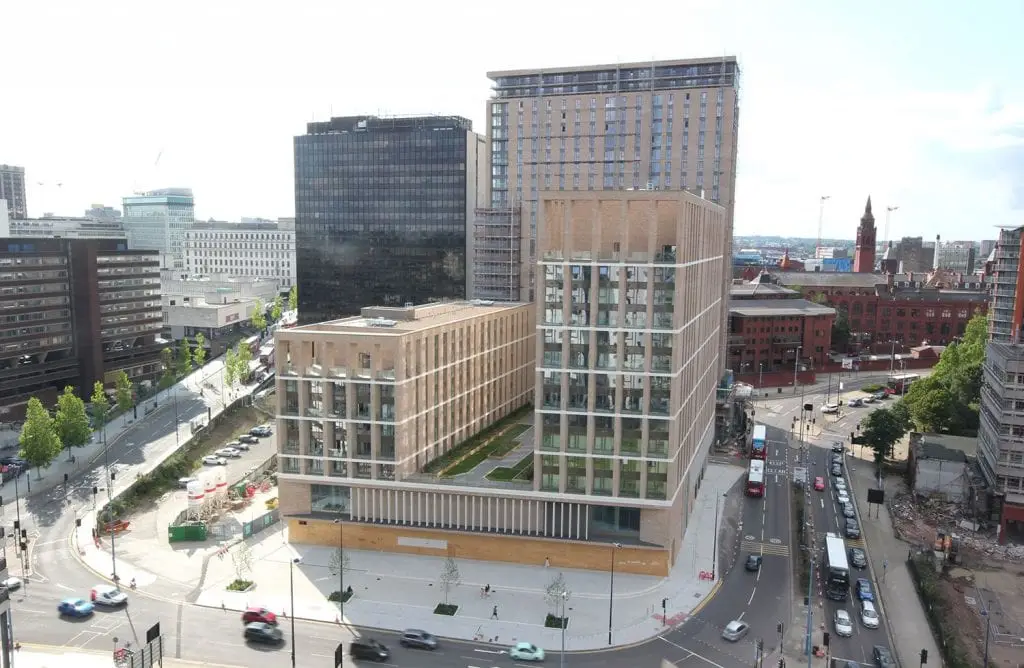
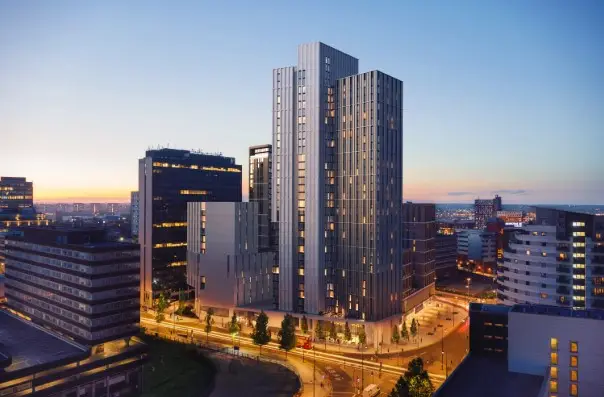
Solutions
IKO Approved Contractor Advanced Roofing turned to the technical team at IKO for specification advice. An inverted roof design was recommended, ensuring all insulation was situated on the outside of the building envelope to avoid any problem with condensation.
IKO’s Hot Melt System provided the answer for the majority of the flat roofs, incorporating IKO Permatec Anti-Root for green roofs, IKO Permaguard Heavy Duty Protection Board for podium roofs and IKO enertherm XPS Insulation Panels.
Where access was more difficult on balconies, IKO Polimar Cold Applied Liquid Waterproofing was used.
All areas needed to meet the same thermal performance, but with different insulation depths. Where level thresholds were required, the slimline IKO enertherm Vacuum Insulation Panel (VIP) was incorporated into the roof system.
The installation, which took place over a two-year period, provided logistical challenges for the contractor: working at height, with restricted access and often in less than ideal weather conditions.
Site cranes took the Holt Melt boilers to the upper floor, while balconies (a total of 45 over 15 floor levels) were accessed either from scaffolding or via the interior – requiring considerable co-ordination with the construction
team.
IKO worked closely with Advanced Roofing throughout, providing detailed specification and technical support.
Contracts Manager Shane Connelly acknowledged the importance of this support: “From specifications to onsite assistance IKO are always on hand to assist with any technical assistance from U-values to wind calculations and changes in specification to meet new regulations and onsite demands.”
The result is an effective, high-performance roofing solution with the reassurance of BBA approved system with a 20-year materials, workmanship and design single point guarantee.