EPDM, or ethylene propylene diene monomer membrane, is one of the most popular single-ply membranes for residential and commercial low slope and flat roof systems. EPDM is essentially a synthetic rubber, making it an extremely durable roofing solution.
The membrane has high resistance to UV radiation and remains flexible even at low temperatures. EPDM Is not inherently fire resistant, however, some membranes offer variations that are fire retardant. Some formulations have heat and chemical resistance.
EPDM membranes are cold applied, avoiding hot air welding or the requirement for a flame. This makes them popular for self-build projects. The lightweight and flexibility of the membrane allow for a relatively simple and precise installation using water-based adhesives and a brush or a roller.
The installation speed is ideal for larger projects. The precision that can be achieved makes EPDM an effective solution for roofs with a lot of detailing, external and internal corners, kerbs and upstands, and a variety of roof penetrations.
EPDM is a single-ply membrane, traditionally laid over timber decks or timber manufactured decks such as oriented strand board (OSB).
Some EPDMs can be bonded with a lightweight concrete deck and non-porous substrates such as fibreglass. Thermal insulation boards with suitable facings and sufficient compressive and interlaminar strength can be overlaid with EPDM directly.
EPDM is a popular solution for new roofs, but it is also the go-to solution in roof refurbishments. The membrane can be bonded with a variety of surfaces. We already mentioned the types of the roof deck and insulation EPDM could be used in conjunction with. In addition, glass, GRP, metal, felt, or asphalt substrate can be overlaid with EPDM.
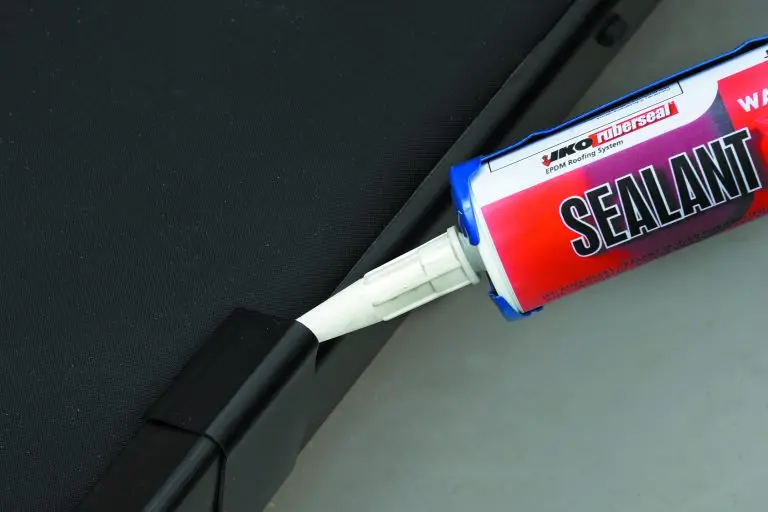
Before we consider the benefits of each roof membrane type, we will have a closer look at how they are manufactured. EPDM is synthesised from petroleum by-products. The synthesised rubber membrane is durable and flexible. PVC is a thermoplastic that can be melted at high temperatures, moulded into the required shape and properties, and then cooled back to a solid form.
The question of being better is hard to answer. The selection of a suitable membrane for a specific roof will depend on the type of roof system, the building use and other project particulars, and external factors such as weather conditions.
Pros
EPDM
Cost effective
Long lasting (>20 years)
Large sheet size, fewer seams
Relatively easy to install
Durable
Resistant to fire
PVC
Long lasting (>20 years)
Chemically resistant
Fire resistant
Strong bond (hot-air welded seams)
UV resistance reduces over time
Cons
Not resistant to animal and vegetable oils
More expensive
Not compatible with asphalt materials
Can crack in cold temperatures
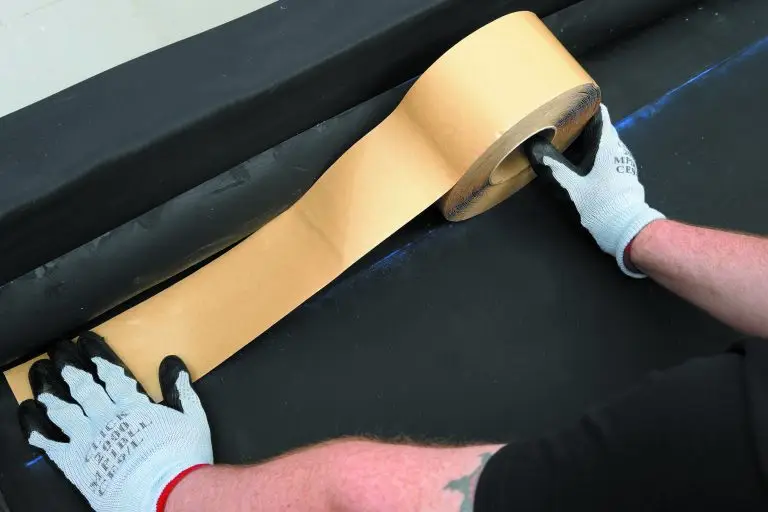
For new roofs that require a durable, long-lasting solution that is easy to install, EPDM membranes are amongst the most economical solutions. They are also repairable, whilst PVC membranes lose the ability to be hot welded over time.
EPDM is also cost effective in roof refurbishments. Unlike PVC membranes that need to be stripped back, EPDM can be bonded with various substrates, making the installation speedy and cost effective.
To learn more about IKO EPDM roofing products, their application and benefits, visit our dedicated EPDM roofing page, or contact us for more information or advice for your next project.